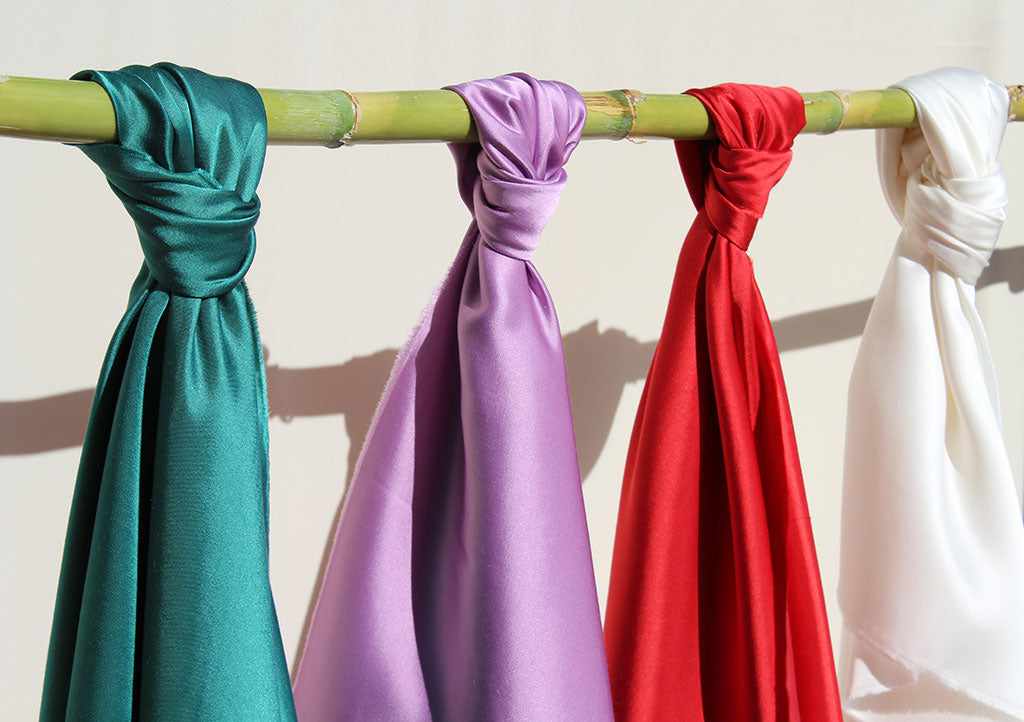
Triacetate: Sustainability in Synthetics
Combining the functionality and durability of a synthetic fiber with the comfort and sustainability of a natural fiber, triacetate has been gaining popularity across the fashion industry.
What is triacetate?
Triacetate is an improved form of acetate. It is a type of fiber known as a semi-synthetic, meaning that the raw material is natural, but processing with chemicals is required to create a usable fiber. Triacetate is made from combining wood pulp from trees with acetic acid.
The fabric is soft, wrinkle-resistant, has a great drape, and is easy to care for. This makes it a more comfortable and more eco-friendly option than many synthetics.
Triacetate vs regular acetate
Triacetate is really just an improved variation on acetate. Within standard acetate, at least 76% of the cellulose hydroxyl groups are acetylated. In triacetate, that number is above 92%. This makes triacetate a stronger, more durable fiber, especially when wet. In addition, triacetate can withstand higher temperatures without melting than regular acetate.
Origins of triacetate
Acetate, which was developed as a more affordable alternative to silk, was patented in 1894. However, it wasn’t produced commercially until after World War I, where it was made by a British company. Acetate was first commercially produced in the United States in 1924, where it gained the trademark name of Celanese.
These days, acetate is produced by many different manufacturers under many different names.
Where was triacetate first produced?
While triacetate was actually first developed around the same time regular acetate was being developed, it was originally a hard plastic that wasn’t commercially viable for making fabric. It wasn’t until 1954 that the triacetate we know today first went into commercial production, where it was made as an improved version of acetate. It was first produced by the company Celanese in the U.S. and Courtaulds in the U.K.
Soalon™ triacetate and Mitsubishi Chemical
In 1967, the Japanese company Mitsubishi Acetate (later renamed Mitsubishi Chemical), started producing triacetate. Their version of triacetate was named Soalon™. By the year 2000, Celanese had stopped producing triacetate and Mitsubishi Chemical was the only company still manufacturing it.
Mitsubishi Chemical worked to improve triacetate and the triacetate production process and helped to bring this fabric into high fashion. Today there are other companies producing triacetate, but Mitsubishi Chemical is still recognized as the premiere manufacturer of high quality, sustainable triacetate.
How is triacetate made?
Making triacetate starts with ethically sourced wood pulp, which must undergo processing to become the durable and high-quality fabric we know as triacetate.
Making the fibers
First, wood pulp is combined with acetic acid to produce flakes of triacetate. The flakes are then dissolved into a solvent to form a syrupy liquid, which is filtered before spinning. The solvent used in this process can be reused, helping to create a more sustainable, closed-loop production process.
Spinning the fibers
The filtered, viscous liquid must then be spun into usable fibers. To do this, the liquid is poured through a nozzle with many small holes. This liquid dries as it comes out, and the tiny threads emerging from the nozzle intertwine and wind into a single yarn, brought together by air pressure as they come out from the nozzle.
As the yarns are formed, the quickly evaporating solvent is collected in pipes throughout the manufacturing facility. Once the solvent is collected, it can be recycled and reused for producing another set of yarn.
Mitsubishi Chemical, which is focused on improving sustainability throughout their manufacturing process, not only reuses their solvents, but also remelts and reuses flawed yarn, majorly reducing waste.
Weaving the fibers
Once the yarns have been formed, wound, and packaged, they are sent to a factory for weaving. The first step at the weaving factory is for the yarn to be twisted. Once it has been twisted, it is sorted into the appropriate types of yarns for forming the warp threads of the fabric. Next, the loom is prepared for weaving and workers program the computers controlling the loom to create the specific type of fabric that is needed. The computer-controlled mechanical loom can then weave the undyed yarns into fabric.
Once woven, the fabric must be carefully inspected for flaws. Acceptable fabrics are sent for dyeing.
Dyeing the fibers
The dyeing process starts with the grey, undyed fabrics received from the weaving factory. First, any starches and oils must be removed from the fabrics before dyeing. Next, the fabrics are dyed at a high temperature to allow the dye to really set into the fibers. Creating the correct color requires the perfect combination of dyes, dye time, temperature, and more.
Once the triacetate has been dyed, it is allowed to dry, then is heated one more time to get any shrinkage out of the fabric before it is shipped to customers.
Is triacetate sustainable?
Triacetate, like all its semi-synthetic cousins (including rayon, lyocell, bamboo, and more), has its downfalls from a sustainability perspective. Chemicals and processing must be used to form triacetate fabric.
However, it is a much more sustainable fabric than most fully synthetic fibers, since the base material forming triacetate is wood pulp sourced from natural trees. In addition, manufacturers with a focus on reducing waste and impact on the environment can further improve the manufacturing process to make it even more sustainable.
Mitsubishi Chemical, the premier manufacturer of triacetate, has an entire program focused on producing their Soalon™ fibers using sustainable methods. Already, they are working towards closing the loop in their triacetate production process by reusing solvents and recycling flawed yarn back to the beginning of the process. Now, they are identifying ways to further reduce the environmental burden of Soalon™ production and are maintaining transparency by labelling their fabrics with a classification based on environmental impact.
Their class III Soalon™ is the most sustainable Soalon™ they offer, while class I, though still a relatively sustainable choice, is the least sustainable of their lineup. Mitsubishi Chemical is working to increase the amount of class III fabrics they offer.
Characteristics of triacetate fabric
Triacetate is a high-quality fabric that makes for wonderful garments and a great wearing experience. Here are 10 key characteristics of triacetate fabric.
- Wrinkle-resistant: Triacetate maintains its shape well and is very resistant to wrinkling, making it perfect for everyday wear and travel clothing.
- Shrink-resistant: Since triacetate is heated and pre-shrunk at the factory before shipping, you won’t need to worry about it shrinking in the wash after you receive it.
- Durable: Triacetate is a more durable alternative to regular acetate; it also maintains its strength when wet, unlike acetate.
- Silk-like luster: Since acetate and triacetate were formed as an alternative to expensive natural silk, they both have a beautiful luster and silky feel, lending to a luxurious look.
- Beautiful drape: Triacetate has a gorgeous, silk-like drape, making it perfect for drapey blouses and eveningwear.
- Can be ironed: Regular acetate is very sensitive to heat and may melt when ironed. Triacetate can handle much higher heats and can be safely ironed on a medium heat setting.
- Maintains beautifully crisp pleats: One of the most desirable characteristics of triacetate is its ability to hold pleats. Many synthetics and semi-synthetics don’t hold pleats well, but when pleats or creases are ironed into triacetate, it will maintain them well through many washes.
- Dries quickly: Triacetate doesn’t absorb as much moisture as many other fabrics, and it also dries very quickly. You can quickly dry your triacetate fabrics in a cool-temperature dryer.
- Holds dye well: When dyed with heat, triacetate holds dye well. This helps to make a variety of rich, deep colors available.
- Easy care: Last, but certainly not least, triacetate is super easy to care for. Its wrinkle-free nature and ability to be machine washed and dried lead to a worry-free fabric.
What garments can be made from triacetate fabric?
Triacetate is a versatile fabric, great for a range of different types of garments, from everyday wear to fancy evening looks.
Here are a few garment suggestions for incorporating triacetate into your fashion line.
- Evening gown with pleats: Since triacetate holds pleats so much better than other comparable fabrics, try using it for a pleated evening gown. You’ll get beautiful pleats with a silky, elegant fabric.
- Drapey blouse: The nice drape of triacetate would make for a great flowy blouse.
- Silky cocktail dress: Triacetate would be a wonderful choice for a silky cocktail dress with a luxe look and feel without difficult care requirements.
- Comfortable, casual skirt: A casual, silky midi-skirt give an everyday outfit a high-end look.
- High-end collared shirt: Triacetate would be the perfect choice for a collared, button-up shirt that needs an extra-special touch of silky luster and a beautiful drape.
Sourcing triacetate fabric
Ready to add this sustainable fabric to your fashion line? We offer a huge selection of luxurious, silky triacetate satins in a range of gorgeous colors – perfect for the elegant dresses and skirts you’ve been dying to create!